Anti-static Protection in the electronics industry, where cleanrooms are essential for manufacturing or assembling sensitive components, electrostatic discharge (ESD) poses a significant challenge. ESD can damage electronic components if not properly managed. Accumulated static electricity in cleanrooms not only affects product quality but also increases production costs due to product damage. This article elaborates on effective methods to prevent ESD in cleanrooms, helping to minimize risks in your production process.
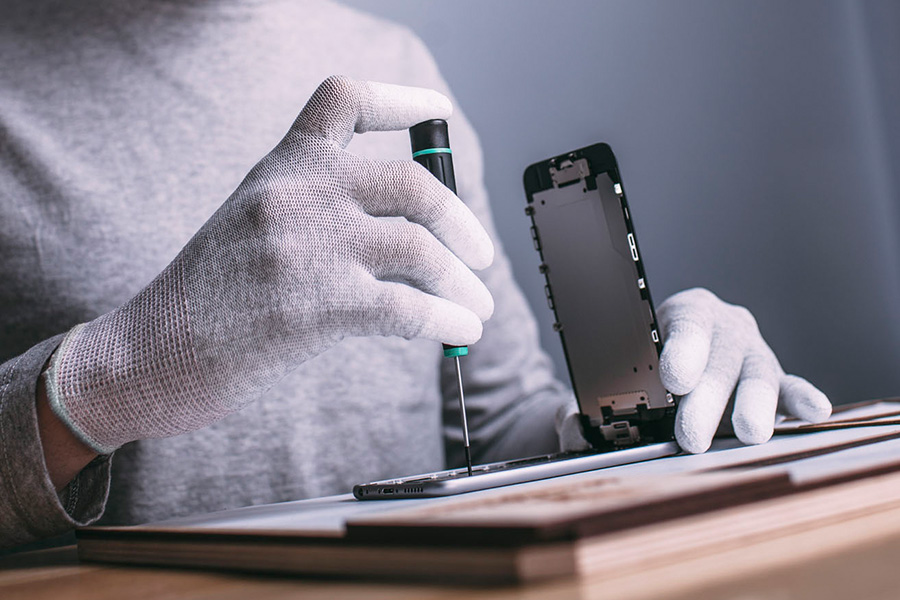
1. Controlling Air Humidity Controlling air humidity is a key factor in preventing ESD in cleanrooms. Low relative humidity (below 30%) increases the likelihood of static charge accumulation, as dry air facilitates the generation of static electricity on surfaces. Maintaining humidity levels between 40-60% effectively reduces the risk of static electricity buildup.
In cleanrooms, using HVAC systems in conjunction with humidifiers can help regulate humidity to optimal levels. Additionally, installing hygrometers at various points in the cleanroom ensures consistent humidity levels. Proper humidity control not only reduces the risk of ESD but also enhances production efficiency.
2. Using Ionizers Ionizers are effective devices for mitigating ESD issues in cleanrooms. They work by releasing positive and negative ions into the air, neutralizing static charges on surfaces or in the air. This balance helps minimize the risk of ESD that could potentially damage electronic components.
Ionizers should be strategically installed, such as in assembly areas or locations prone to static buildup. Portable ionizers can also be used in specific spots requiring precise control. Employing these devices not only reduces ESD risks but also helps maintain cleanliness in the cleanroom.
3. Wearing Personal ESD Protective Equipment Wearing personal ESD protective equipment is a crucial measure for cleanroom personnel. ESD-safe cleanroom suits, made from materials designed to reduce static charge accumulation on the body, play a significant role. Accessories such as gloves, shoes, and headcovers with conductive properties further enhance protection against static buildup.
ESD protective suits should be regularly inspected and maintained to ensure effectiveness. Wearing these garments not only reduces the risk of static discharge affecting products but also enhances safety for individuals working in ESD-sensitive environments.
4. Designing Employee Movements Employee movements within cleanrooms can be a source of static electricity. Activities such as walking, standing up, or handling equipment improperly can generate static charges. Designing proper movement protocols and training employees to move cautiously can help mitigate this issue.
Encouraging slow walking on ESD floors and avoiding unnecessary rubbing of objects or surfaces can significantly reduce static charge buildup. Awareness and adherence to ESD control practices contribute to long-term process stability and product quality.
5. Installing ESD Flooring ESD flooring is another critical component in preventing static electricity in cleanrooms. Made from materials that dissipate static charges to the ground, ESD flooring minimizes the risk of static discharge affecting electronic components.
Selecting the right material for ESD flooring depends on the nature of the work and the cleanroom environment. Proper maintenance, such as cleaning with non-damaging substances, ensures the longevity and effectiveness of ESD flooring.
6. Using Anti-static Sprays Anti-static sprays provide a quick and easy method to reduce static charge accumulation. Spraying these substances on surfaces of machinery, equipment, or areas prone to static buildup forms a thin film that prevents static accumulation and discharge.
Choosing anti-static sprays that are compatible with the materials and do not affect product quality is essential. Regular application enhances the overall effectiveness of ESD control in the cleanroom.
Preventing ESD in cleanrooms for the electronics industry requires attention to every detail, from environmental control and technological aids to proper employee training. Each of these methods plays a vital role in reducing ESD risks, ensuring smooth and efficient production processes while maintaining the highest product quality.